Congratulations to Keller ASEAN on setting a new record of 650 days without a lost-time injury (LTI). How did they do it? Regional HSEQ Manager Malcolm Loke explains how four critical injuries set the business unit on the road to improvement – and how he plans to keep everyone focused on an injury-free future.
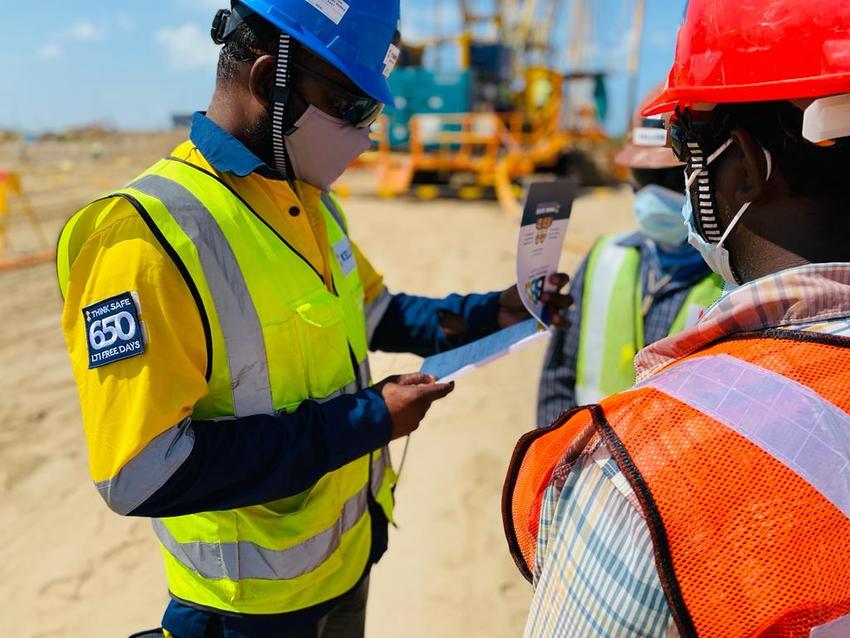
It was early 2020 when Keller ASEAN suffered four major on-site injuries in a period of just two months, prompting a full-scale, management-led investigation into the business unit’s safety processes and systems.
“One of the root causes for the injuries was that, as we took on more projects and introduced new products, we also took on a lot of new temporary workers who simply weren’t as familiar with our processes and safety culture,” explains Malcolm. “So one of the main things we’ve improved since then is the training to ensure everyone working on Keller projects is trained and clear on the rules, processes and expectations.”
Cultural change
Malcolm says that since those accidents, there’s been a transformation in culture, led from the very top. Leadership has taken part in safety meetings and site inspections, and introduced on-the-job training and assessment programmes, safety KPIs for managers and rewards for employees reporting hazards.
“We’ve really increased our near-miss and hazard reporting, so that any potential problems are rectified in due time before they can escalate, while fundamentals like 5S have greatly reduced the risks of small hazards like trips and falls,” he adds.
Malcolm also believes having a strong, competent core safety team across ASEAN countries has ensured processes are implemented on the ground.
This intense focus on improving the safety culture over the past two years has resulted in an accident-frequency rate of zero and clocked up 650 LTI-free days across more than 20 projects.
Building on success
While everyone at ASEAN is delighted with the results, Malcolm is keen to ensure that no complacency creeps in and they can keep building on the record. As such, he has introduced five areas to focus on this year:
- Risk management: Identifying potential areas of risk such as the use of unfamiliar new products, non-routine activities, night work and near-misses, along with integrating lessons learnt from previous incidents.
- Strengthening processes: Reviewing existing systems, auditing safety processes to ensure they’re as strong as possible and being implemented correctly, and standardising good practices across ASEAN.
- Competency and training: Assessing employees to ensure they’re up to speed, and developing people’s awareness and skills.
- Leadership: Leaders continuing to lead safety programmes, take part in safety walks and maintain communication.
- Behavioural-based safety: Ensuring the BBS observation programme is ingrained to a higher degree through trend-based campaigns, KPIs and on-site observations.
As Malcolm prepares for his latest campaign focused on avoiding back injuries, he says that safety is about persistence and constant communication. “Safety is not a short-term initiative, it’s about having a consistent, long-term focus – only then can we sustain this culture.”