Jet Grouting uses high velocity fluid jets to construct cemented soil of varying geometries in the ground.
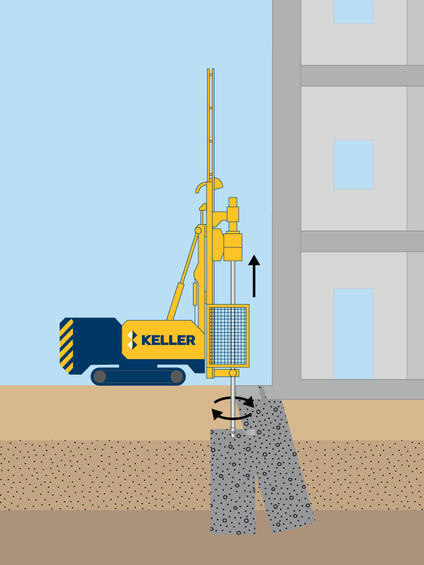
Common uses
Process
Jet grouting creates in situ geometries of soilcrete (grouted soil), using a grouting monitor attached to the end of a drill stem. The jet grout monitor is advanced to the maximum treatment depth. Then high velocity jets (cement grout with optional water and air) are initiated from ports in the monitor. The jets erode and mix the in situ soil with grout as the drill stem and monitor are rotated and raised.
Depending on the application and types of soils, one of three variations is used: the single fluid system (slurry grout jet), the double fluid system (slurry grout jet surrounded by an air jet) and the triple fluid system (water jet surrounded by an air jet, with a separate grout port). The jet grouting process constructs soilcrete panels, full columns, or partial columns with designed strength and/or permeability.
The soilcrete geometry and physical properties are designed based on the in-situ soils. Because it is an erosion-based system, soil erodibility plays a major role in predicting geometry, quality, and production. Cohesionless soils are typically more erodible by jet grouting than cohesive soils.
Advantages
Quality assurance
With 40 years of experience, working across the globe, Keller has seen and completed more jet grouting projects than any other contractor in the world.
In addition, constant improvements in technology, such as Keller’s proprietary method of determining column diameter: the Acoustical Column Inspector or ACI, ensure project requirements are met.